塑膠射出成型
塑膠主要區分為兩種性質:熱塑性塑膠與熱固性塑膠
熱塑性塑膠與熱固性塑膠
塑膠基本上對溫度有很高的依存性,也就對溫度有所反應,依其反應的不同,大致上可分為熱塑性塑膠與熱固性塑膠二大類:
熱塑性塑膠:加熱熔化,冷卻固化,可反覆為之。
熱固性塑膠:一旦加熱產生分子鍵的交鏈反應並待其固化、硬化後,即不再對溫度有所變化,不因溫度加熱而熔化。
影響塑膠材料特性當中,在其製程當中包含:
- 加工溫度:每種塑料有其合適的加工溫度範圍,溫度太低則流動困難無法充填,溫度太高則可能造成熱裂解。
- 流動速度:流動時會因速度的分佈梯度而產生不同程度的剪切率,剪切率低則靠近模壁附近的皮膚層塑料容易造成滯流現象,導致充填困難,但是若速度太快造成的剪切率太高,則會造成剪切應力的高速增加,將使塑膠高分子的分鍵過度拉伸甚至被扯斷,造成斷鍵現象,或產生過度摩擦熱(黏滯產生的蓄熱效應)而造成塑料的熱裂解。
- 體積收縮:在相變化過程中所產生的比容變化,可參閱PVT圖,將使熔融的塑料產生體積的改變。
- 冷卻速率:熔融的塑料冷卻應有適當的模溫,低模溫雖可縮短成型週期,但若冷卻太快將降低結晶程度,很大程度的狀況下,且易產生應力殘留。
- 應力殘留:流動時的分子拉伸,保壓時的壓力過度過高,冷卻時因冷卻不均所造成的熱應力與收縮應力。
- 頂出溫度:每種塑料都有其適當的頂出溫度範圍,而頂出溫度是指其肉厚的中心層溫度,必須冷卻到塑料擁有具有足夠的剛性溫度後,才不會在頂出時造成變形或頂白,一般選擇是在塑料的熱變形溫度之下。
熱塑性塑膠的主要成型加工方法
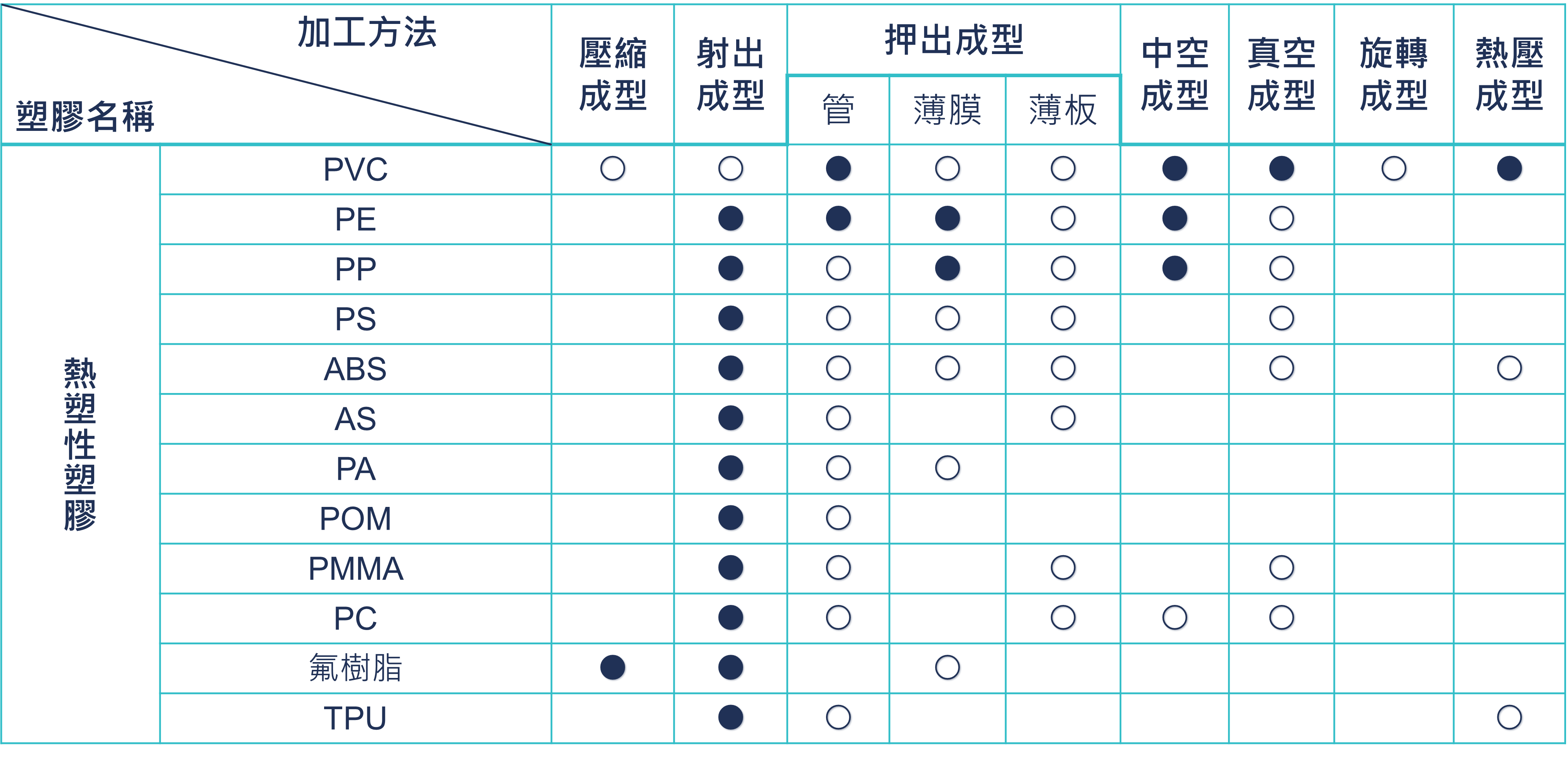
熱固性塑膠的主要成型加工方法
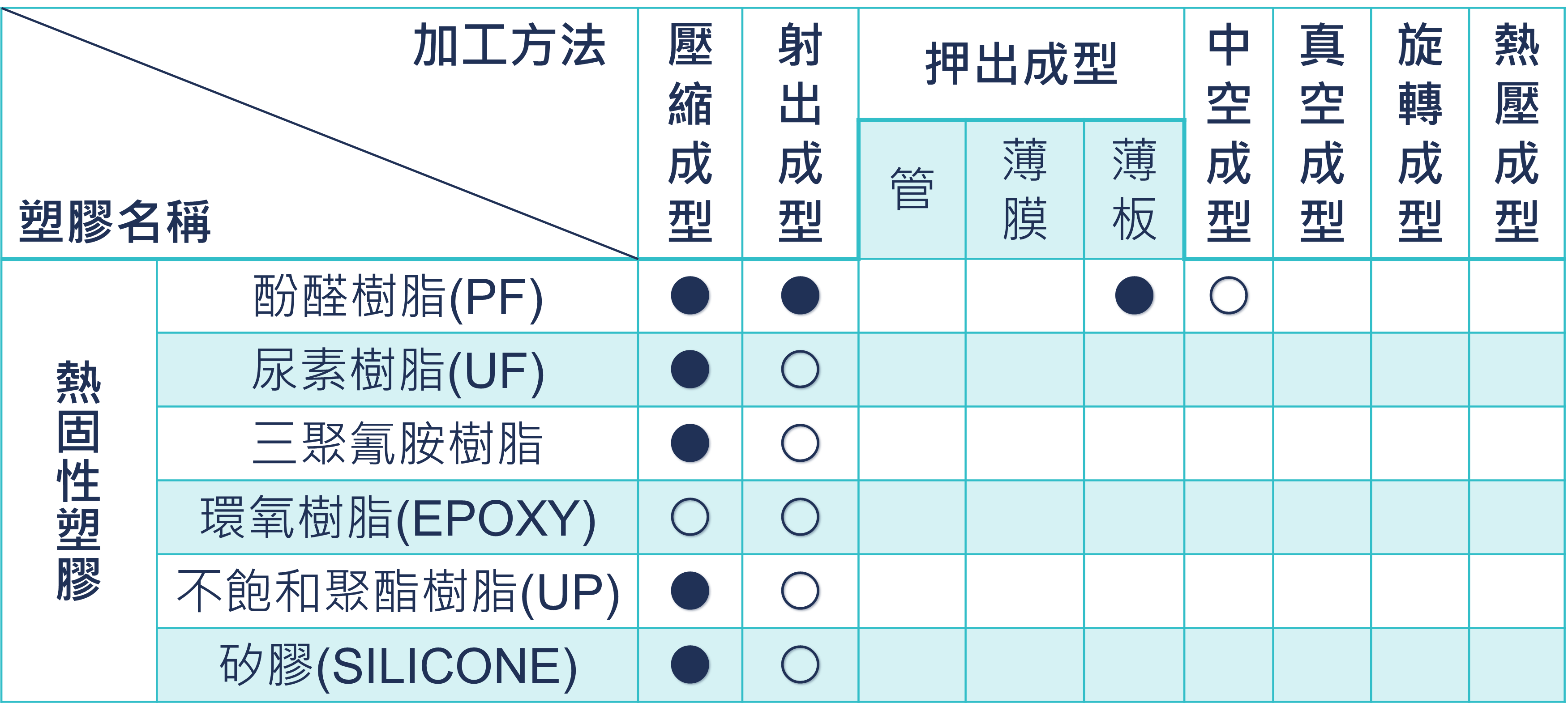
塑膠射出是什麼? 射出成型製程與加工法
塑膠製品在所有人的生活週遭中非常的常見,如我們每天都在使用的3C產品,如手機外殼、電腦外殼、滑鼠等等;日常用的居家產品,如保鮮盒、隨身水瓶;甚至大到連汽機車外殼面板、戶外型家具等,都會使用到各種不同類型的塑膠,塑膠材料應用廣泛的程度早已融入我們的生活中,可以說是息息相關,而大部分的熱塑性塑膠都適用於射出成型的加工方式,然而在各種類型的塑料卻都具有不同的特性,在生產過程中必須考慮這些不同的特性。射出成型是一個高量產性的循環過程,包括進料、熔融、塑化、壓力注射(射出、擠壓、保壓)、模具冷卻,開模後,最後就是成品零件的取出等多個階段的塑料加工,必須考慮每個步驟對最終產品的影響。
塑膠射出成型的優點
- 產量高、生產速度快
- 材料價格低廉、選擇性高
- 可回收利用(熱塑性材料)
- 輕量化
- 可自動化生產
- 機構設計之搭配性高
塑膠射出成型
- 射出成型機結構與規格功能介紹
- 射出成型的加工原理
- 射出成型的流動與各項關聯
- 穩定的成型條件與多段充填與多段保壓
- 射出成型的常見不良問題
- 其它加工與製程原理介紹
- 氣體輔助射出成型、雙色或多色射出成型、微細發泡射出
塑膠射出成型流程
塑膠射出成型過程,主要可分為5個步驟:塑化 ⇒ 射出⇒ 保壓 ⇒ 冷卻 ⇒脫模,這5個階段在製造過程中會持續循環,配合上自動化生產趨勢,可以高效率的大量製作出所需要的塑膠製品。
1.塑化
將塑膠原料在料管中以高溫溶化,依照選擇的塑膠材料特性,在射出成型機台上設定塑料加工溫度,讓塑膠粒在正確的溫度下融化。
2.射出
透過螺桿將融化的塑膠原料充填射出至模具中,利用模具設計空間將塑料定型,這時候必須依照塑膠射出成形條件或是模具狀況適當的調整射出機參數,避免後續產生尺寸不合、毛邊、缺料等不良問題。
3.保壓
塑膠原料充填至模具後,對模具內的空間繼續加壓,主要是確保這些塑膠原料充填的緊密度,避免原料回流,避免產品發生缺料、尺寸不足等問題。
4.冷卻
產品在模具內快速冷卻定型並接續做下一模次的塑化階段。
5.脫模
最後塑膠製品完成,打開模具,將產品自模具取出。